1, hvernig á að stjórna snúningsáttskrefmótor?
Þú getur breytt stefnumerki stjórnkerfisins. Þú getur stillt raflögn mótorsins til að breyta stefnunni á eftirfarandi hátt: Fyrir tveggja fasa mótora er aðeins hægt að skipta um annan fasa skrefmótorsins, eins og A+ og A-. Fyrir þriggja fasa mótora er ekki hægt að skipta um annan fasa mótorsins, heldur ætti að skipta um fasa í röð, eins og A+ og B+, A- og B-.
2, hinnskrefmótorHávaði er sérstaklega mikill, enginn kraftur og titringur mótorsins, hvernig á að gera það?
Þessi staða kemur upp vegna þess að skrefmótorinn vinnur í sveiflusvæðinu, lausnin.
A, breyttu inntaksmerkistíðninni CP til að forðast sveiflusvæðið.
B, notkun undirdrifs, þannig að skrefhornið minnki og gangi vel.
3, þegarskrefmótorEr kveikt á, mótorásinn snýst ekki, hvernig á að gera það?
Það eru nokkrar ástæður fyrir því að mótorinn snýst ekki.
A, snúningur sem hindrar ofhleðslu
B, hvort mótorinn hafi skemmst
C, hvort mótorinn er í ótengdu ástandi
D, hvort púlsmerkið CP sé núll
4, þegar stepper mótorinn er kveiktur á, mótorinn titrar og gengur ekki, hvernig á að gera það?
Ef þetta gerist skaltu fyrst athuga hvort tenging mótorsins og drifbúnaðarins sé röng, svo sem tengingin, og síðan athuga hvort inntaks púlsmerkistíðnin sé of há og hvort hönnun lyftitíðninnar sé ekki sanngjörn.
5, hvernig á að gera gott starf við lyftihreyfilinn?
Hraði skrefmótorsins breytist með púlsmerkinu sem kemur inn. Fræðilega séð er hægt að gefa drifbúnaðinum púlsmerki. Með því að gefa drifbúnaðinum hvern púls (CP) snýst skrefmótorinn um eitt skrefhorn (skipting skrefhorns). Hins vegar, vegna þess að afköst skrefmótorsins breytast of hratt, mun skrefmótorinn ekki geta fylgst með breytingum á rafmagnsmerkjum, sem leiðir til stíflu og skrefataps. Til að skrefmótorinn geti verið á miklum hraða verður að vera hraðaaukningarferli, og við stöðvun verður að vera hraðalækkunarferli. Almennt séð gilda sömu lögmál um hraðaaukningu, sem dæmi er eftirfarandi hraðiaukning: hraðaaukningarferlið samanstendur af stökktíðni og hraðakúrfu (og öfugt). Ræsitíðnin ætti ekki að vera of stór, annars mun það einnig leiða til stíflu og skrefataps. Hraðaupp- og niðurfærsluferlarnir eru almennt veldisvísisferlar eða leiðréttir veldisvísisferlar, en auðvitað er einnig hægt að nota beinar línur eða sínusferla o.s.frv. Notendur þurfa að velja viðeigandi svörunartíðni og hraðaferil í samræmi við eigin álag, og það er ekki auðvelt að finna kjörferil og það krefst venjulega nokkurra tilrauna. Veldisvísisferillinn er erfiðari í raunverulegu hugbúnaðarforritunarferlinu, almennt reiknaðir fyrirfram tímafastar sem eru geymdir í minni tölvunnar, og vinnuferlið er valið beint.
6, stigmótorinn er heitur, hvert er eðlilegt hitastigssvið?
Of hár hitastig skrefmótors mun afsegulmagna segulmagnaða efnið í mótornum, sem leiðir til lækkunar á togkrafti og jafnvel taps á skrefi. Þess vegna ætti hámarks leyfilegt hitastig ytra byrðis mótorsins að ráðast af afsegulmagnspunkti mismunandi segulefna. Almennt séð er afsegulmagnspunktur segulefna yfir 130 gráður á Celsíus, og sum jafnvel hærri. Því er það fullkomlega eðlilegt að skrefmótorinn birtist við 80-90 gráður á Celsíus.
7, hver er munurinn á tveggja fasa skrefmótor og fjögurra fasa skrefmótor?
Tveggja fasa skrefmótorar hafa aðeins tvær vafningar á statornum með fjórum útgangsvírum, 1,8° fyrir allt skrefið og 0,9° fyrir hálft skref. Í drifinu er nóg að stjórna straumflæði og straumstefnu tveggja fasa vafninganna. Þó að fjögurra fasa skrefmótorar í statornum hafi fjórar vafningar, eru átta vírar, allt skrefið er 0,9° og hálft skref er 0,45°, en drifbúnaðurinn þarf að stjórna fjórum vafningunum, sem gerir rafrásina tiltölulega flókna. Þannig að tveggja fasa mótorar með tveggja fasa drif, fjögurra fasa átta víra mótorar hafa samsíða, raðtengda og einpóla tengingu af gerðinni þrjár. Samsíða tenging: Fjórfasa vafningar tvöfalda, vafningsviðnám og spanstuðull minnka veldishraða, mótorinn gengur með góðri hröðun, miklum hraða og miklu togi, en mótorinn þarf að tvöfalda nafnstrauminn, hita, sem samsvarar aukningu á afkastagetu drifsins. Þegar notað er í röð eykst vindmótstaða og spann veldishraða, mótorinn er stöðugur við lágan hraða, hávaði og varmamyndun er lítil, kröfur um drif eru ekki miklar, en togtapið við háhraða er mikið. Þannig geta notendur valið fjögurra fasa átta víra skrefmótor í samræmi við kröfur.
8. Mótorinn er fjögurra fasa sex línur og hvernig á að nota fjóra línuna til að keyra skrefmótorinn?
Fyrir fjögurra fasa sex víra mótor er miðtappa tveggja víra sem hanga ekki tengdur, en hinir fjórir vírarnir og drifbúnaðurinn eru tengdir.
9, hver er munurinn á viðbragðsstigmótorum og blendingstigmótorum?
Blendingsmótorar eru ólíkir að uppbyggingu og efni og eru úr efni af varanlegum seglum að innan, þannig að blendingsstigmótorar ganga tiltölulega vel, með miklum sveiflukrafti og litlum hávaða.
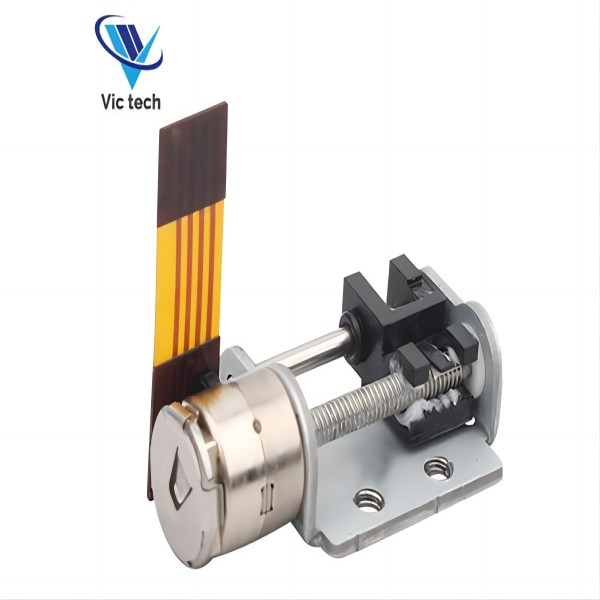
Birtingartími: 16. nóvember 2022